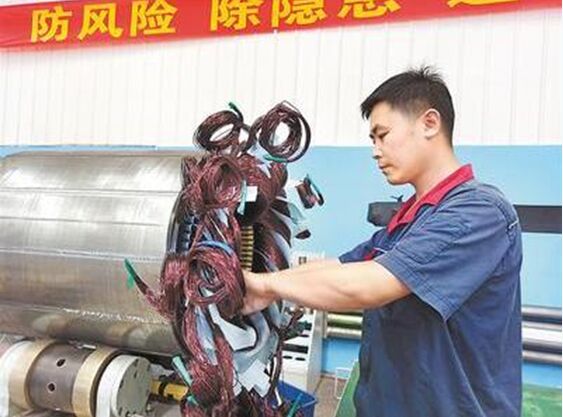
9月1日,河北电机股份有限公司员工正在变频高效高压电机数字化车间进行电机生产。
9月1日,走进位于石家庄市栾城区的河北电机股份有限公司变频高效高压电机数字化车间,只见车间内上料、生产、组装、喷涂各道工序都在紧张有序进行。 在车间的定子嵌线区,公司员工武海辉正在通过智能终端扫描线圈上的条码。显示屏上,线圈信息和他需要进行的工作一一显示。他告诉记者:“以前原材料寻找、交接,工作布置需要较长时间。进行数字化改造后,这些环节变得很顺畅。” 瞄准全球供应链高端市场,河北电机是生产超高效节能电机、专用特种电机产品的电机专业制造企业,为压缩机、水泵、制冷、减速机、电梯、印染等行业国际领先企业提供产品和服务,产品出口美国、加拿大等20多个国家和地区。 他们发现,大中型电机制造逐渐向单机容量大、特殊化、多样化、定制化方向发展,且变频调速技术产业化还不够理想。2016年开始,他们开展了变频高效高压电机数字化车间建设,加大变频高效高压电机生产。该项目于2018年全部完成。 如今,漫步在车间,只见监测设备密布于生产线各节点,10多个智能终端对应着不同的工位,从德国进口的生产设备正在进行定制化产品生产。 “数字化改造花费了900多万元,加上这些制造设备,整个车间投资总额接近1亿元。这个车间展示了我们最先进的制造水平。”河北电机IT中心主任石欣介绍,车间实现数字化,首个环节是把企业资源计划(ERP)、制造执行系统(MES)、分布式控制系统(DCS)三个系统进行融合。这也是整个过程的难点所在。 ERP负责外部订单处理和库房物料管理,DCS负责底层各类设备的联网与通信,MES负责车间现场执行过程管控,对上接收ERP订单数据,对下集成DCS系统,实现设备连接与控制指令下发。 通过和来自北京、南京的技术团队进行联合攻关,他们确定了三系统的融合方案:不同系统之间采用先进的WEB服务作为统一集成接口,方便相互调用;数据统一采用标准格式,便于解析和交换,提高传输效率。经过大量试验,系统终于实现了有机融合。 数字信息的实时获取也是数字化改造的关键。 在这方面,他们通过在生产线和车间的各关键工位和节点设置多个信息采集点,实现了智能感知和在线监测。 两个关键步骤和一些后续环节完成后,车间就实现了“管控一体化”:经营计划、采购、物料、生产、库存、销售、财务等实现了动态监控。同时,车间的物流、信息流、控制流和资金流实现“四流合一”。 如今,在这个车间,刷一下卡就能知道自己该做什么。 结合MES、PDM(产品数据管理)、ERP系统,数字化车间实现了电子工单自动发放到工位,工人在电子终端上刷卡就能接收到当班工作任务,图纸和作业指导书也会跟随工单同时下发。 变化不止于此。 通过ERP和MES,车间实现了物料按工位拣选配送,通过条码等工具,配送过程实现了高效、精确。 车间也变得透明。通过网络、传感器、智能终端,车间实现了对设备、物料、人员等车间现场信息的实时采集,实现生产过程透明化。 管理者也能体会数字化带来的便利。车间的生产进度、工时统计、质量状况、设备运行状况等数据经过组织梳理后,能够根据需要的样式,以报表、统计图等方式在监控大屏上进行展示,实时反映车间的生产状况,便于生产主管及时掌握作业情况。 “变频高效高压电机数字化车间建成后,生产过程实现可视、可控,产品实现了可追溯,产品质量、生产效率均得到大幅提高。”该公司变频高效高压电机数字化车间项目经理范立欣介绍。相比以前,数字化车间生产效率提高20%,运营成本降低15%,产品生产周期缩短30%,产品不良率降低15%。车间每年为企业节省600万元成本,增加约1000万元销售额。 在该车间,记者看到,来自阿特拉斯、英格索兰、格兰富、西门子等国际巨头的订单产品正在紧张生产。通过数字化车间建设,河北电机产品的竞争力得到大幅提高,订单不断。
|