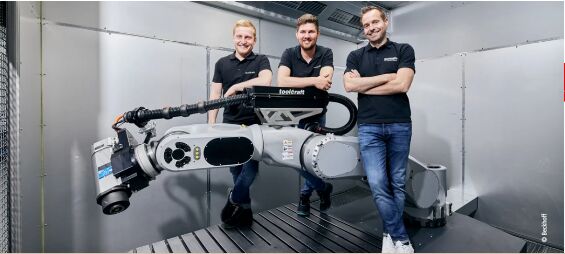
如果有人认为,使用关节臂机器人无法完成硬质材料的精密加工,那么 toolcraft 公司就会用事实证明他们的观点是错误的。Daniel Distler 和 Andreas Bauer 使用倍福的 TwinCAT CNC 和基于 PC 的控制技术,让机器人单元能够精密加工包括碳化硅和灰铸铁实心棒在内的零部件。
与五轴数控系统一样,操作和轨迹规划也通过 G 代码进实现,并在定制的 CP3921 多点触控控制面板上实现可视化。
toolcraft 清楚地了解加工制造业的需求,哪些工艺和技术在实践中有效,哪些无效。因为 toolcraft 不仅使用其 60 台 CNC 机床为客户进行生产,而且还为各个行业的企业设计、规划和建造交钥匙生产系统。
toolcraft 公司成立于 1989 年,起初是一家合同制造商,后来逐步增加了各种制造服务,比如在 2005 年新增了注模和模具制造服务,以及在 2011 年新增了增材制造服务。2015 年,机器人技术成为 toolcraft 最新的技术部门。“无论我们在哪种技术领域开展业务,我们都希望拥有提供完整解决方案所需的专业知识。”机器人技术部门经理 Daniel Distler 解释道,他主要负责公司的销售和人事工作。
其产品范围包括各种简单设备以及可集成到客户现场现有系统中的复杂系统。“配备新技术的设备与最终客户的现有控制系统之间的连接并不总是那么容易,但如果采用灵活的控制技术,就能轻松做到。”toolcraft 机器人技术(工程)部门经理 Andreas Bauer 说道。
适用于各种应用的自动化平台
这就是 Andreas Bauer 和 Daniel Distler 依赖基于 PC 的控制技术的原因,例如在生产单元中使用七轴铣削机器人进行 CNC 零件加工。“TwinCAT CNC 是第一款集成连接史陶比尔机器人控制器(TwinCAT Robotics uniVAL PLC,TF5130)的接口的控制器。“在项目实施过程中,这个软件包为我们实带来了很多便利。”Andreas Bauer 回忆道。目前,有个用户正在使用 toolcraft 设计的加工单元用大型碳化硅和灰铸铁块铣削加工晶圆生产底座。“在这方面,toolcraft 已经在使用我们的 TwinCAT CNC。”倍福纽伦堡分公司销售 Alexander Klos 补充道。
样机的整个控制和监测系统都在搭载 Intel® CoreTM i7 CPU 和四个处理器核的 CX2040 嵌入式控制器(左下)上运行。
最初,客户仍然使用传统的五轴 CNC 机床加工金属块。但铣削硬质材料时会产生极细的粉尘,这些粉尘会渗透到每个接缝处、直线导轨和轴承中,短时间内就会造成很严重的问题。CNC 机床很快就出现了磨损,需要进行大修。“我们当时就知道,使用 TwinCAT CNC 后,我们就可以在大到 1 立方米的加工区域内实现 2/10 毫米的高精度,同时还能对史陶比尔机器人进行密封并施加超高压。”Daniel Distler 强调道。这些技术知识积累来自各个项目,例如,在这些项目中,机器人被完全拆解并密封,即使在水深达 20 米的情况下仍能可靠运行。
新一代数控机器人
机器人在零件加工中有着巨大的潜力,但应该把重点放在哪里呢?“我们对机器人铣削的发展方向进行了长时间的认真思考,当然还有如何实现发展。”Daniel Distler 解释道。我们的目标不仅是进一步提高加工质量,将其提升到一个新的水平,而且还要确保用户在创建加工程序时不会有任何改变。在 2018 年项目开始时,用“最佳方案”仔细检查了加工单元的所有组件:机器人、旋转工作台、换刀装置、铣削主轴,当然还有控制技术。Andreas Bauer 说道:“从我们过去八年积累的专业知识和经验来看,我们对各种运动学和设计的优缺点了如指掌。”我们与一家机器人供应商合作,利用这些专业知识开发出了能够提高构件刚度、防尘/防水性能、有效载荷以及机械臂伸展范围的运动学功能。
因此,目前的加工单元配置的是基于新型运动学的高端数控机器人。“除了 TwinCAT CNC 之外,toolcraft 还为其新一代数控机器人配备了倍福的伺服驱动器和伺服电机。”Alexander Klos 补仓道。机器人所有轴的驱动和输出端都配备了双轴承齿轮和编码器。此外,还对主轴托架进行了改装。铣削机器人的控制系统基于功能强大的 CX2040 嵌入式控制器和 CP3921-1502-0010 CNC 多点触控控制面板构成,通过 CP-Link 4,只需一根以太网电缆(CAT.6A)即可连接面板与嵌入式控制器。AM8000 伺服电机和 AX8000 多轴伺服系统以及 TwinCAT CNC 使系统更加完善。新设计还包括内置软管,它可以简化搬运工作。此外,它也无需单独的机器人控制器,从而节省了控制柜空间,降低了项目的复杂性。
倍福 AM8000 伺服电机以及驱动和输出端的编码器确保机器人的高精度运动控制。
驱动技术的直接转换
“虽然 toolcraft 一开始使用的是 TwinCAT CNC 和 TwinCAT Robotics uniVAL PLC,但很快就转换到了另一种具有不同机械结构、运动学以及我们的驱动和伺服驱动技术的机器人类型。”Alexander Klos 在指出基于 PC 的控制技术的开放性和灵活性这两个重要特点时说道。例如,可以将机器人轴的驱动和输出端编码器轻松集成到轴控制器的软件功能块中。倍福能够提供从 CNC 系统到伺服驱动器再到电机等各种通用型产品系列,toolcraft 因而可以拥有各种完全不同的优化选项。“直接访问所有参数和过程设置在进一步提高精度方面起到了很大的作用。”Andreas Bauer 说道。例如,通过输出端编码器和适当的控制算法,进一步补偿了虽低但仍能检测到的齿轮滞后现象。即使在施加较大的力时,例如在大规模铣削过程中或根据工作区域中刀具中心点 (TCP) 的位置,也能快速、精确地跟踪轴。“测量和校准周期的整合确保了性能的一致性。”Daniel Distler 补充道。
toolcraft 还可灵活选择反馈系统和使用其它技术:伺服驱动器支持多种编码器接口,还可通过 EtherCAT 提供其它功能选项。“我们凡事都会提前考虑,目前正在考虑集成相机系统,以检测和自动加载零件。”Andreas Bauer 说道。
后处理程序和坐标转换包括在内
对于制造企业来说,重要的是拥有一个从 CAD 图纸到加工程序的有效运转的工艺流程。Daniel Distler 说道:“我们的方法是消除用户对机器人操作和编程的畏惧,同时提供更多的加工自由度。”基于 PC 的控制技术在这方面也发挥了重要作用:后处理程序和坐标转换与数控机器人的轨迹控制同时在嵌入式控制器上运行。因此,加工程序可以像平常一样用 G 代码编程,并从常用的 CAD/CAM 程序生成。Daniel Distler 解释说道:“我们希望机器人能与用户的 CAM 软件完美配合。”toolcraft 为此还提供了灵活的基于 PC 的控制平台。
|